In addition to supplying our own configurable turbomachinery controls products to the compression market, we also deliver integrated application-specific solutions using leading hardware platforms (PLC, DCS, configurable governors, and auxiliary protections).
Brand | Platform(s) |
---|---|
Allen Bradley | ControlLogix, CompactLogix |
Consen Technologies | TSxPlus, TSxElite, TSxSmart |
Honeywell | C300 |
Siemens | S7, PCS7 |
RTP | TSx |
Triconex (Schneider) | Tricon, Trident, Tri-GP |
Tri-Sen | TS3000, TS160, TS310-SC |
We supply both centrifugal and axial compressor controls solutions for Refining, Ethylene, Chemical, Ammonia, Fertilizer, LNG, and Transmission applications
Industry | Plant/Unit/Machine |
---|---|
Refining | Hydroprocessing, Fluid Catalytic Cracking - Power Recovery, Catalytic Reforming, Delayed Coking, Alkylation, Gas Plant |
LNG | Mixed Refrigerant, Propane Refrigeration, Boil-off Gas, Fuel Gas, Treat Gas |
Ethylene | Cracked Gas, C2 refrigeration, C3 refrigeration, Binary refrigeration, Heat Pump |
Ammonia | Process Air, Syngas, Ammonia Refrigerant, Feed Gas |
Fertilizer | CO2, Nitric Acid, Air, NOx |
General | Waste water, pipeline, etc. |
Basic Compressor Throughput (Process, Performance) Control
The most basic compressor throughput control is typically accomplished with: discharge throttling, suction throttling, guide vane positioning, or speed control.
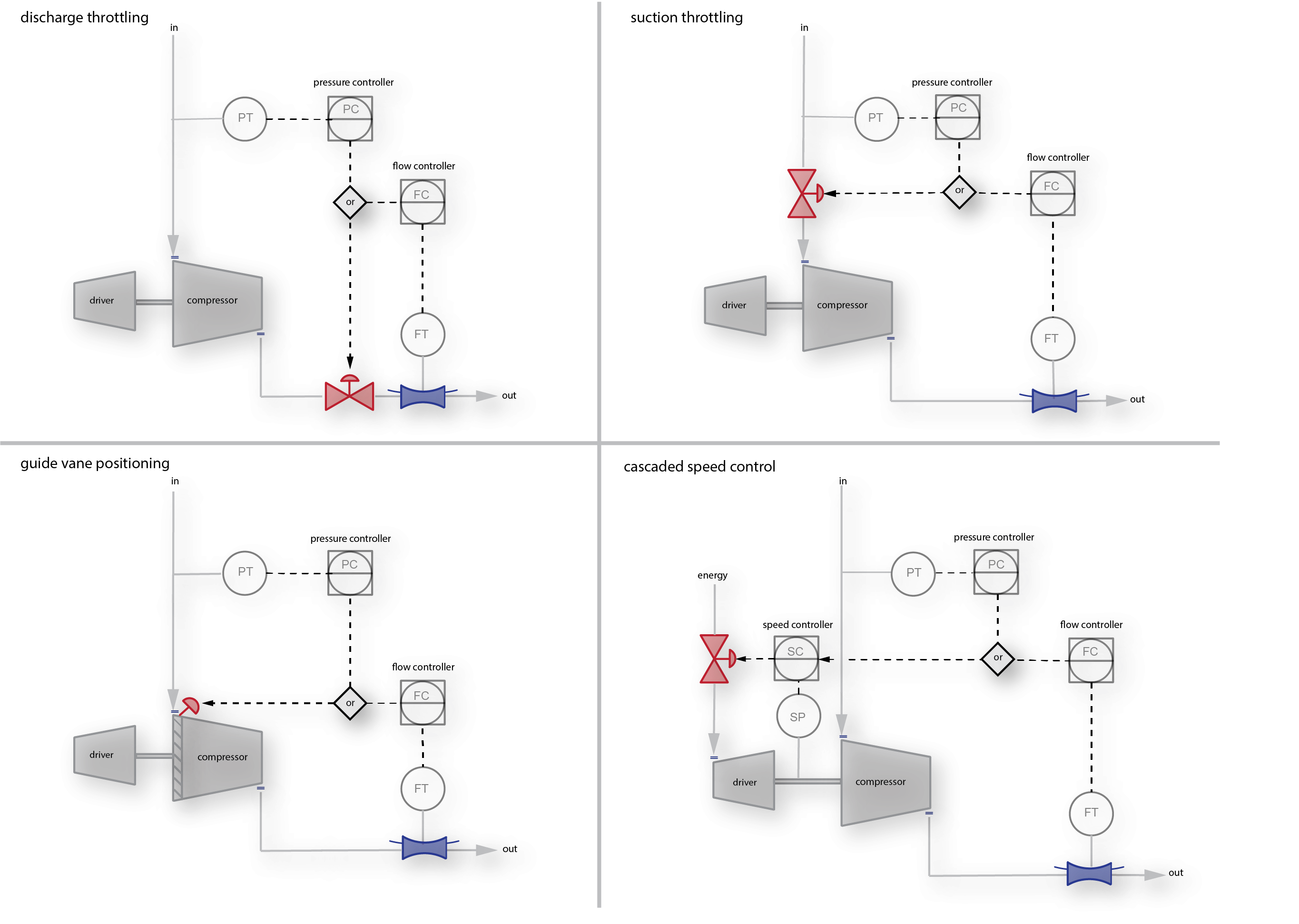
Typical Tri-Sen Basic Compressor Throughput Control includes:
- Automated start-up / shutdown sequencing
- Adaptive PID tuning
- Bumpless transfer between process PID controls
- Bumpless process PID Auto/Manual transitions
- Process limit override controller(s)
- Auxiliary controls (seal gas, lube oil, etc.)
Both centrifugal and axial compressors can be exposed to surge events, which tend to have adverse effects on a compressor's lifetime productivity, and in some instances, the surge event can be disastrous to the compressor.
A surge event is caused by insufficient flow, but using a minimum flow controller to maintain sufficient flow is inefficient and at some operating points, ineffective. The insufficient flow is typically caused by a pressure build-up when a a downstream block or throttling valve closes, but using a maximum pressure controller to relieve the compressor discharge pressure is also inefficient and at some operating points, ineffective.
The Tri-Sen surge controller protects the compressor from surge events by continually calculating an operating limit to the right of, and parallel to, the compressor surge limit for all operating conditions. Then the controller ensures that the current compressor operating point stays "to the right of" the operating limit, by modulating the compressors recycle/blow-off valve(s).
Tri-Sen Anti-Surge Control Features:
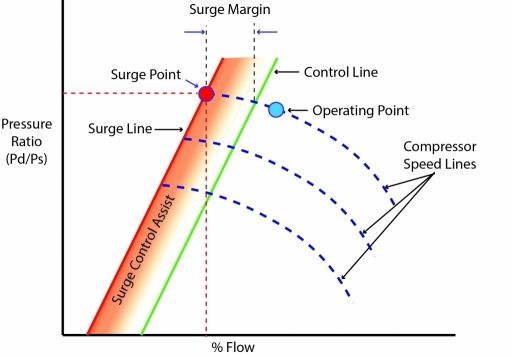
Basic Anti-Surge Control
The primary function of the anti-surge control is to prevent the compressor from operating in an unstable surge region (left of the surge line). Continued operation in a surge region can result in process disruption and compressor mechanical failure. Anti-surge control prevents surge from occurring by maintaining a minimum flow rate through the compressor. This minimum flow rate is assured by modulating a “spillback” (recycle,) or vent valve (anti-surge control valve).
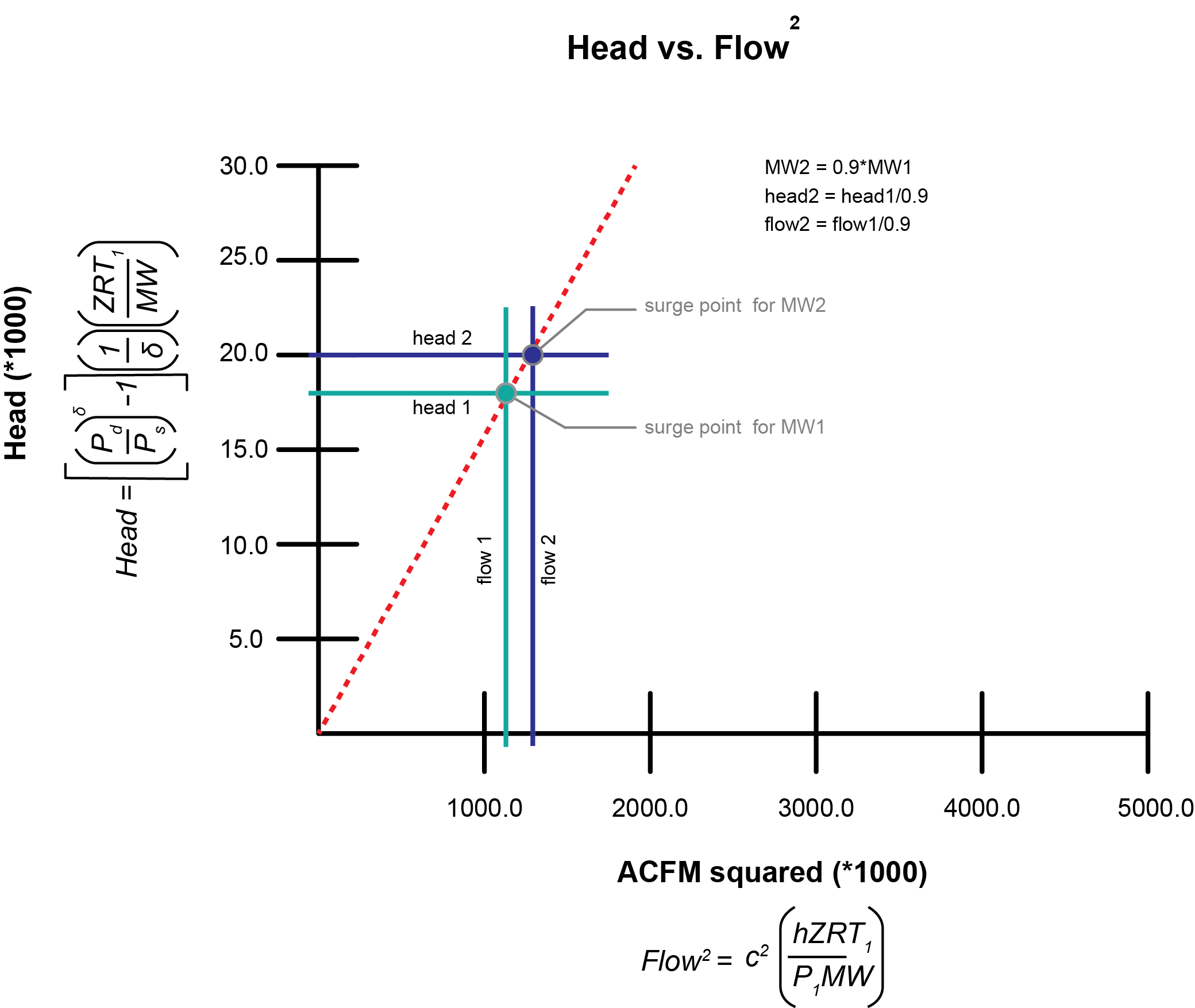
Reliable Surge Line Prediction
Any changes to the molecular weight will affect the head term in the same way that it affects the flow term. So if the molecular weight drops the head will increase and the flow will also increase. The new surge point will fall on the same line.
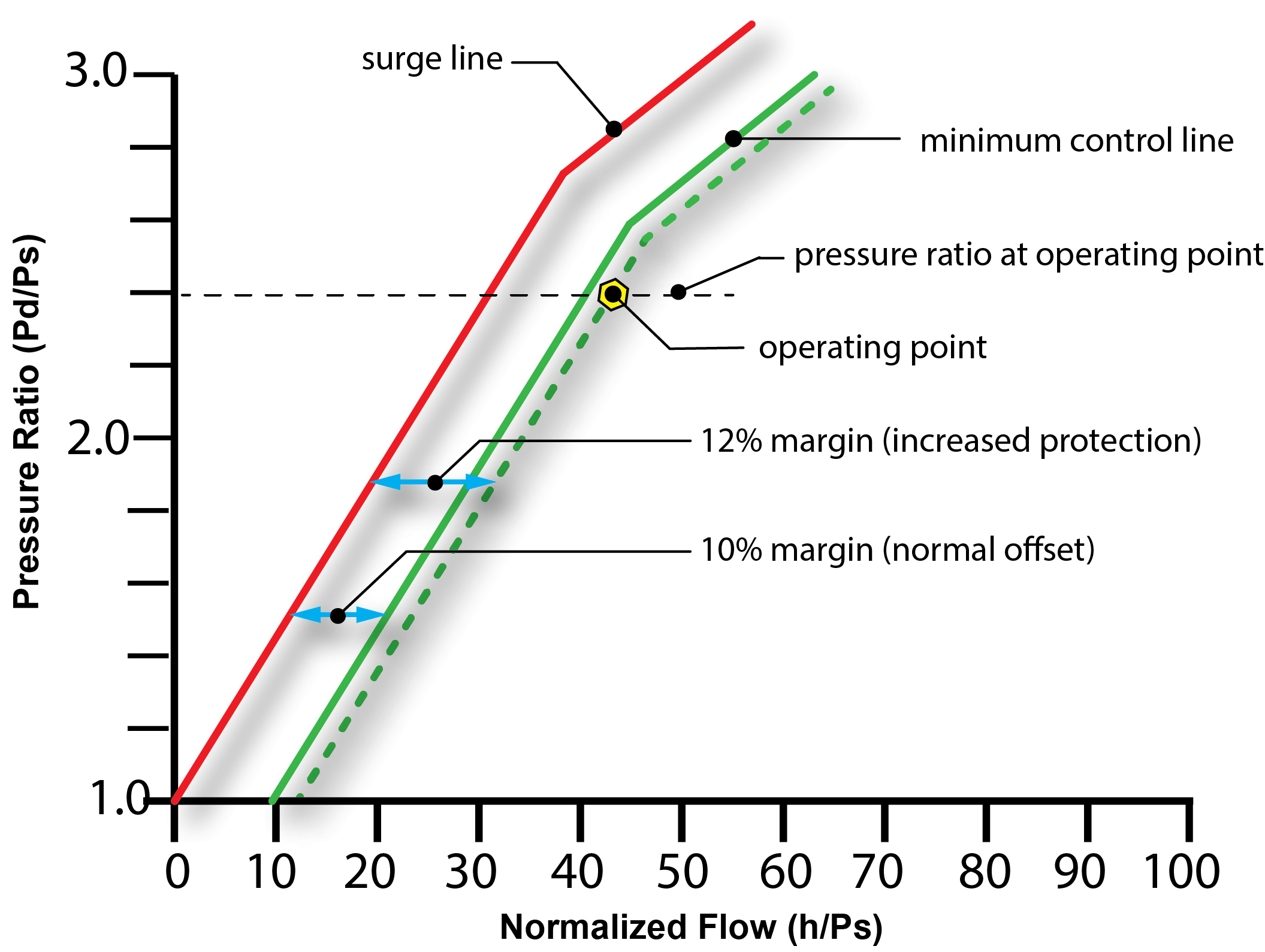
Adaptive Control Line
- Configurable increase in margin if surge occurs
- Provides added protection in the presence of a system failure
- Protected reset
- Generates operator alarm and increments surge count
Selectable Control Modes
Full Manual: In full manual control you have complete manual control of the Anti-Surge control valve. In full manual control mode, the anti-surge control PID tracks the manual control valve position to ensure a bumpless transfer when the anti-surge controller is enabled.
Full Auto: In full auto control, the Tri-Sen anti-surge controller has full automatic control of the anti-surge control valve.
Cooperative Auto: In the cooperative auto control mode, you can manipulate the anti-surge control valve manually; however, the anti-surge controller prevents you from closing the anti-surge control valve such that the current operating point would be to the left of the minimum control line.
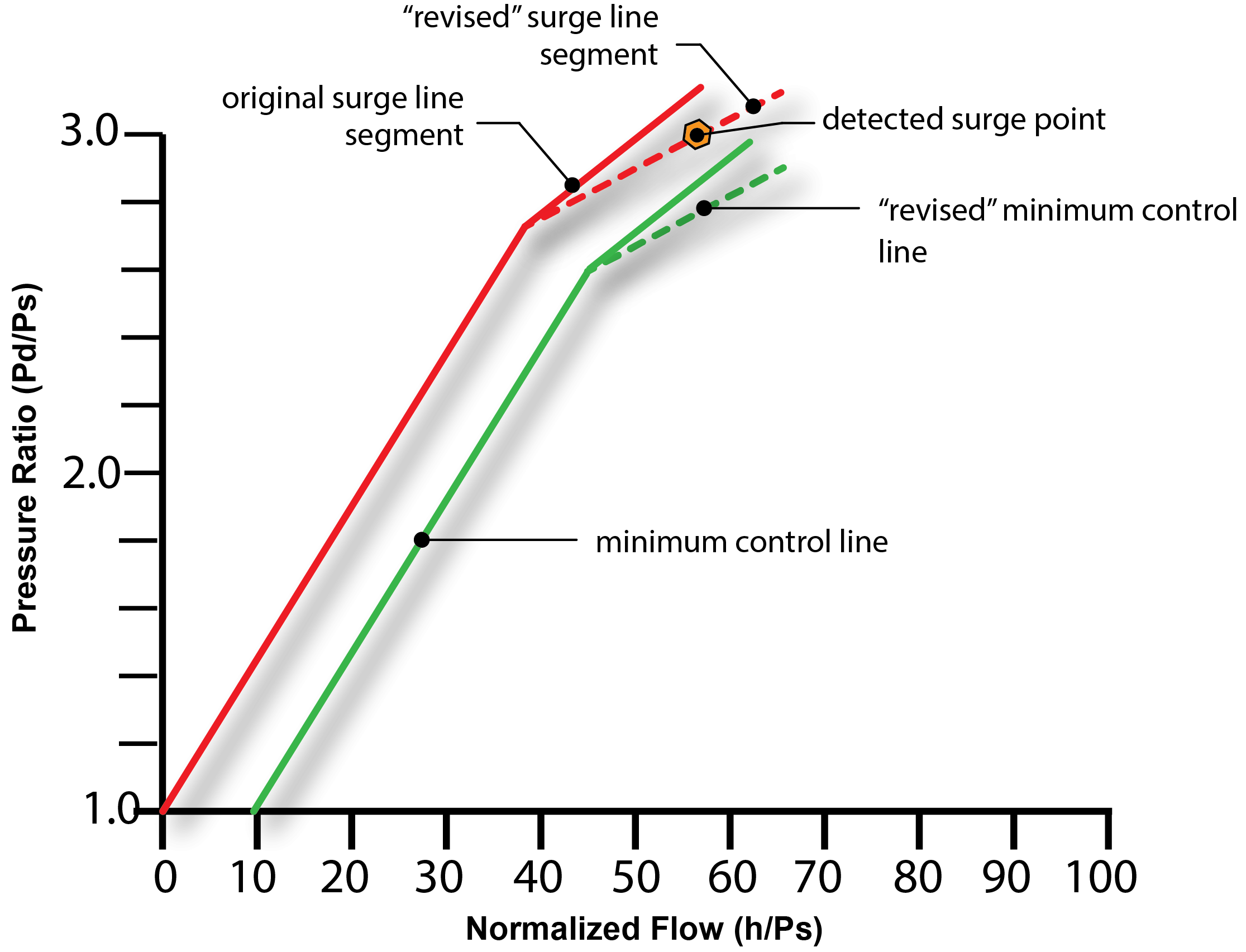
Automatic Surge Line Update
- Automatically adds a detected surge point to the surge line and redraws line
- "Memorizes" pressure ratio and reduced flow when a surge occurs
- Accommodates inadequate surge testing
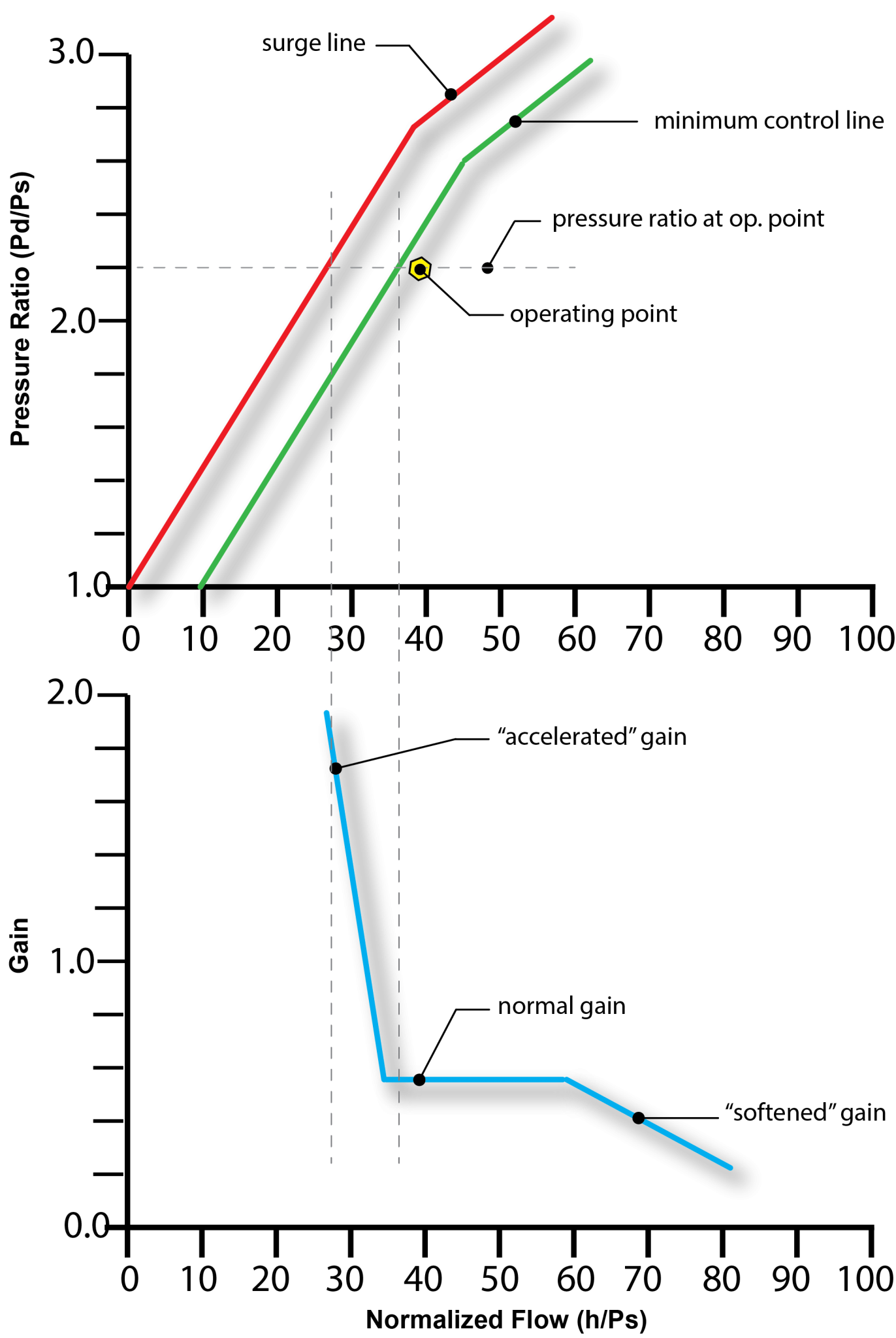
Adaptive Tuning
- Allows appropriate tuning for normal operation
- Adaptive tuning for either gain term (proportional), reset term (integral), both, or neither
- Can be configured to drive valve closed quickly if surge margin is high
- Applies more aggressive tuning if operating point drops below minimum control line

Surge Control Assist
The surge control assist (SCA) ensures the anti-surge control valve is opened independently of the anti-surge PID when the operating point is to the left of the control line. The SCA increases the output to the anti-surge control valve exponentially as the operating point moves closer to the surge line.
Tri-Sen Anti-Surge Control Features Summary
- Surge line prediction: (invariant to changes in gas conditions) – accurate surge line prediction regardless of changes to suction density
- Adaptive control line: increases minimum safety margin if operating point reaches surge line
- Selectable modes: Full manual, Full Auto and Cooperative Auto
- Automatic Surge Line Update: surge line is updated with surge points detected during operation.
- Adaptive Tuning: Applies more aggressive gain and integral when operating point moves too close to the surge line
- Surge Control Assist: fast opening, slow closing of the anti-surge control valve
Both the throughput controller and the anti-surge controller are continually trying to position the compressor operating point, and the action of each controller affects the other. These interactions, if not considered, can cause uncontrollable noise or continuous oscillations. The severity of the interaction depends upon; relative controller gains, respective loop periods (closer periods tend towards more severe interactions), and whether the controls action is conflicting or cooperative.
Conflicting control action is most dangerous for the anti-surge controller because the throughput controller output tends to push the operating point left, towards the surge curve at the same time the anti-surge controller is trying to prevent a surge event.
This conflicting control action is alleviated through the implementation of "decouple" controls. This decoupling of controllers forms the "anchor" of an integrated controls solution.
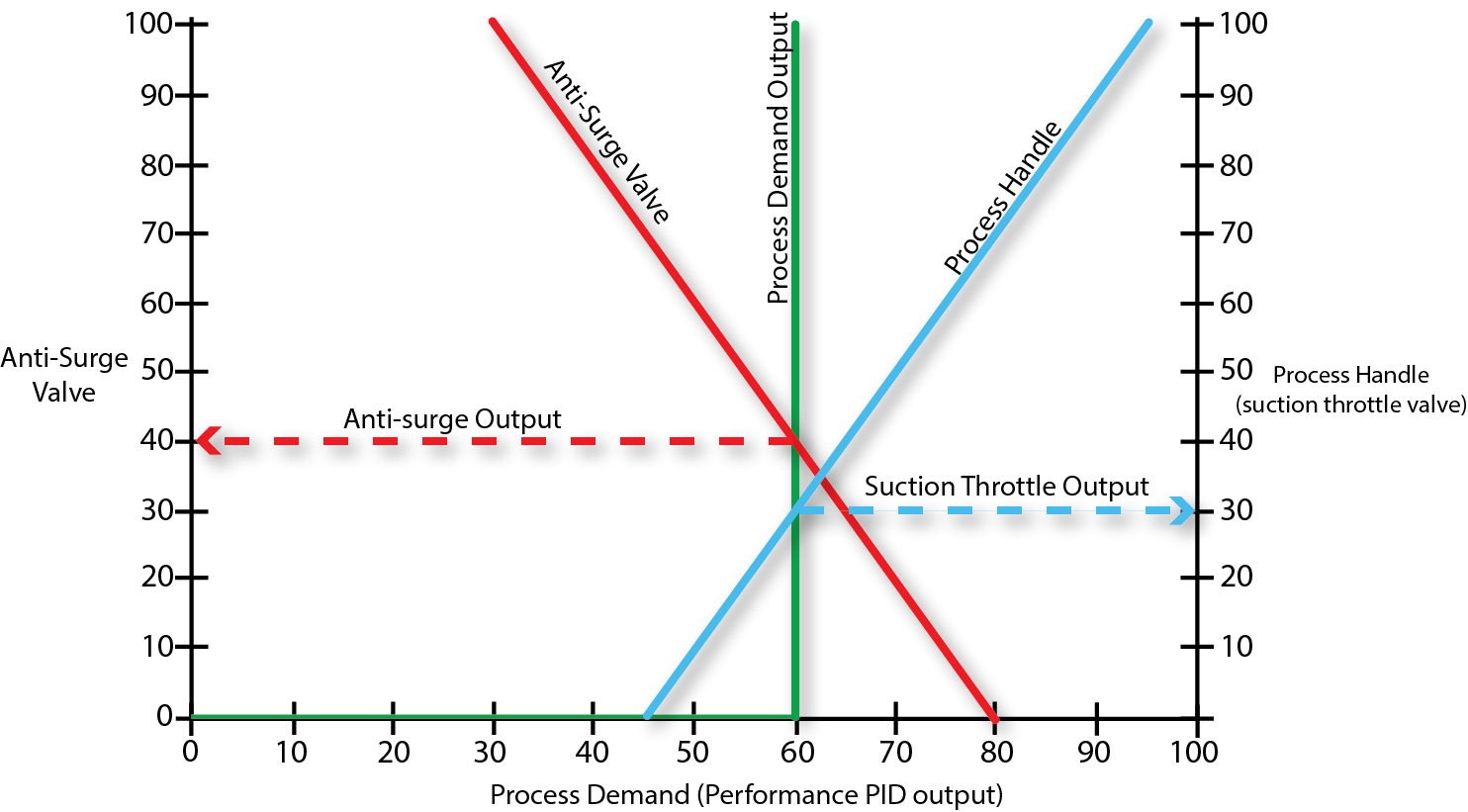
Process Demand Scheduler PDS
The Process Demand Scheduler (PDS) is a standard feature that is included with our compressor control systems that are also managing process performance. The PDS function provides a coordinated means of using the anti-surge valve along with another process control function (speed, suction throttle valve, guide vane) to manage the process. The PDS prevents the anti-surge controller from interacting with the process controller, expands the control range of the process controller and uses the anti-surge recycle valve to absorb significant process load disturbances.
Tri-Sen Integrated Controls Solutions Features (typical)
- Unit start-up and shutdown sequencing
- Anti-Surge Control
- Performance Control
- Seal Gas System Control
- Lube Oil System Control
- Driver Control (Steam turbine, Gas Turbine, Motor)
- Overspeed Protection and Test
- Turbine Auxiliary Controls (Hotwell Level, Condensate System)
- First out alarming and trips
- Power Recovery Turbine Control
- Process Demand Scheduler
When we talk about compressor load sharing, we talk about either serial load sharing or parallel load sharing. Serial load sharing increases compression ratio while parallel compressor load sharing increases flow capacity.
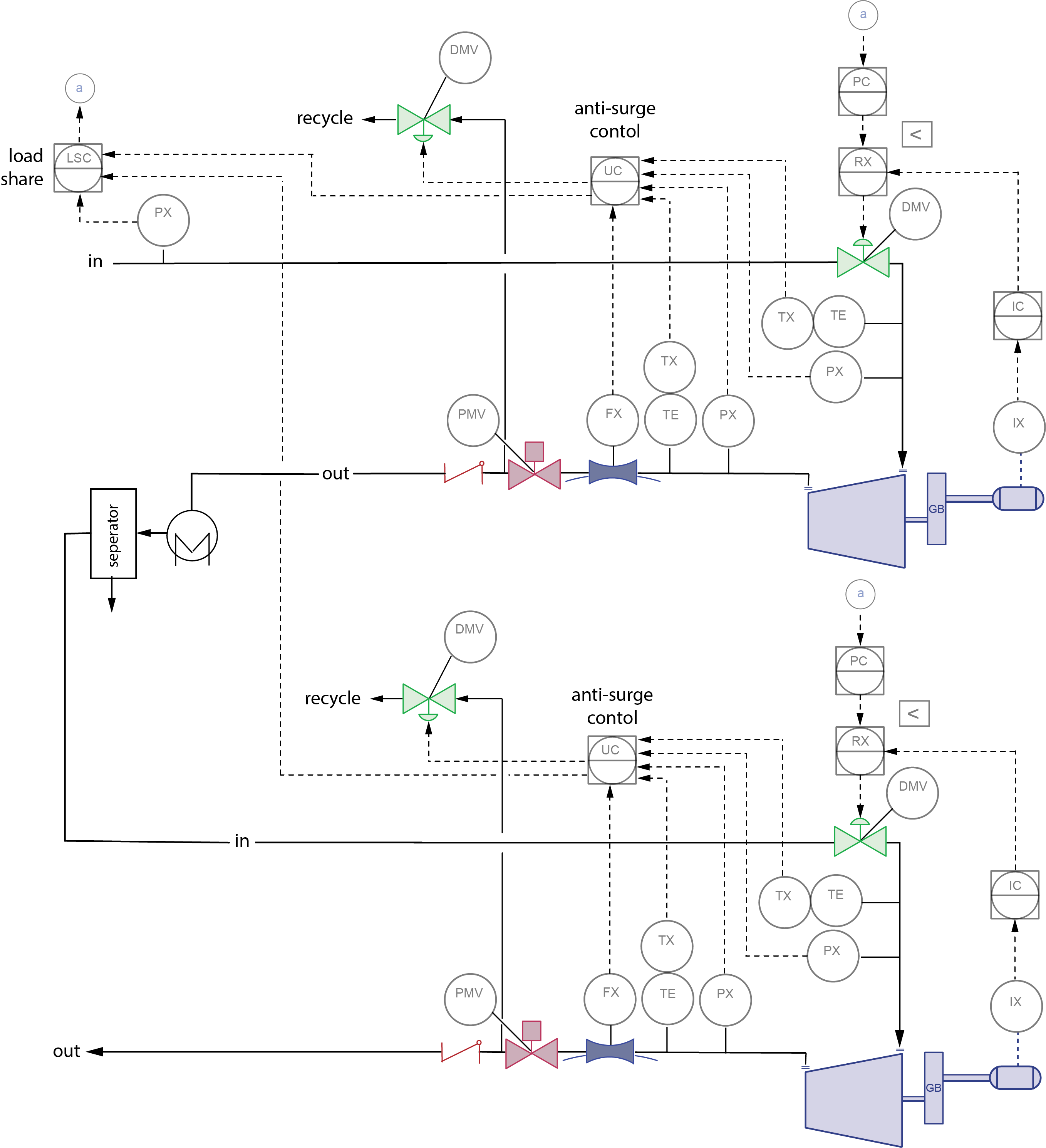
Serial Load Sharing
The Tri-Sen serial compressor load sharing solution is process dependent, and typically modeled/discussed during the front end engineering design of the turbomachinery controls solutions. Typical solutions include: compression ratio division, and speed ratio division.
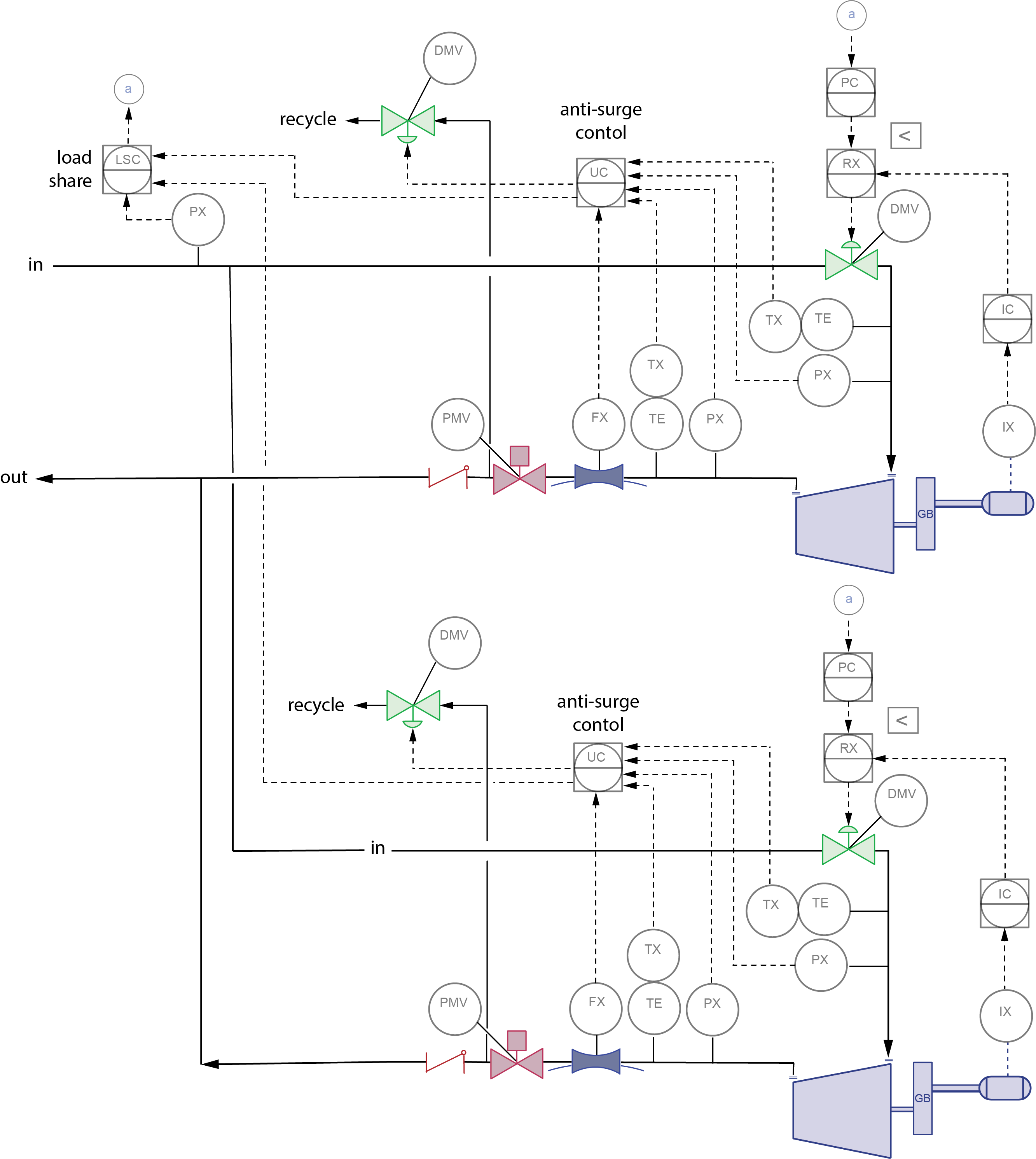
Parallel Load Sharing
The Tri-Sen parallel compressor load sharing solution is process dependent, and typically modeled/discussed during the front end engineering design of the turbomachinery controls solutions. Typical solutions include a simple capacity split (can be weighted) based on the average compressor "distance from surge."
Tri-Sen Load Share Features:
- No dedicated hardware controller required
- Data transferred over high-speed peer-to-peer network
- Balancing managed by Process Demand Scheduler
- Automatically adapts to number of compressors on-line
- Application Load sharing schema validated/demonstrated with "first-principles" simulation before shipping from factory
Check out our blog
Every few weeks, we add a new discussion on a turbomachinery controls topic that we were either asked about recently or a topic that we think you might be interested in learning more about.